GSIクレオス、型内塗装で連携企業体
自動車を取り巻く環境がカーボンニュートラルという概念の登場で大きく変わりつつある。2050年のカーボンニュートラル実現のため、変化が加速してきたのは電気自動車(EV)と言える。EVは単に動力源がバッテリーとモーターに変わるだけでなく、車体にも変革をもたらし、仕上げを担う塗料・塗装の変革が要求される。すなわち、軽量化を図るための素材の変化、CO2削減・コスト削減・工程削減の実現と、従来の〝塗るプロセス〟の流れが一新する可能性が出現してきた。加えて、車の魅力を引き出す豊かな色彩表現による高意匠性、耐擦傷・耐衝撃性といった機能性の要求は変わらず、塗料・塗装への要求レベルは高まる傾向に。技術開発を進める企業の事例としてGSIクレオス(東京)を紹介する。
既存射出成型機でも導入可能
GSIクレオスは、武蔵塗料、金型・成型試作を行う岐阜多田精機と共同で、自動車部品用の型内塗装技術(ColorForm)を自動車メーカー等に提案を行っている。このたび、既存の国産射出成型機(対面2色方式型)でも型内塗装が行える国産の反応型樹脂注入機の提案を新たに開始した。 これにより、型内塗装への導入ハードルを下げ、同システムによる採用拡大を狙う。
GSIクレオスが提案している型内塗装は、自動車製造におけるCO2排出を大幅に削減できる新しい塗装塗膜成形方式である。自動車生産の塗装工程からのCO2排出量は全体の4分の1を占めると言われている。カーボンニュートラル等の観点からも、CO2を削減する新たな塗装代替技術への期待が集まっていた。特に2022年から、環境への取組みが強化されるに連れて、型内塗装への引き合いも増え、既に国内でも採用が始まっている。
型内塗装は、自動車の内外装プラスチック部材の射出成型工程で同じ金型内の平行プロセスで塗膜を形成するもの。既存の塗装ブースが不要となり、細かい温湿度調整や乾燥工程も必要ないことから省エネルギー化を実現する。同時に、既存のスプレー塗装に比べ大幅にCO2排出を抑えられるとしている。型内塗装の材料には有機溶剤を使用しないためVOCの削減効果もある。加えて、型内で全て塗装を終えるため、歩留まり率も高く廃棄物の削減が可能となる。
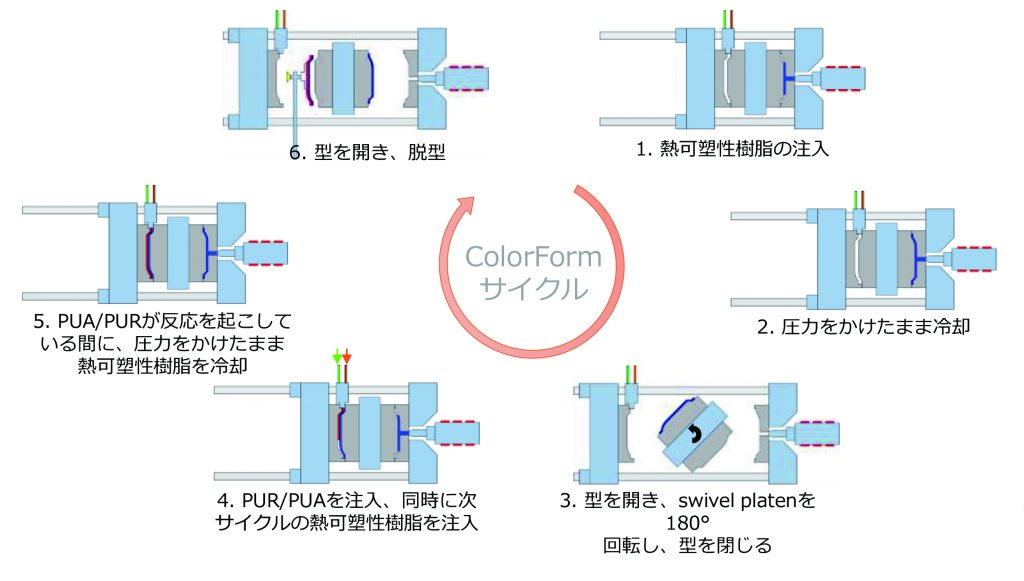
型内塗装技術のイメージ
型内塗装のプロセスは、主剤のポリオールとイソシアネートを金型注入直前で混合させ化学反応により射出成型部材表面に塗膜形成を行う。着色する場合は、顔料分散したポリオールを注入し3液混合により塗膜形成させる。型内では1次材の冷却固化による成型と、2次材の化学反応による塗膜形成をほぼ同じタイミングで終わるように全自動で制御され、成型サイクルとして50~90秒で完了する。なお、既存の射出成型機(対面2色方式型)でも型内塗装が行えるよう、国内需要に合わせて樹脂注入機を製造し、既存の製造設備でも型内塗装が行えるよう配慮した。
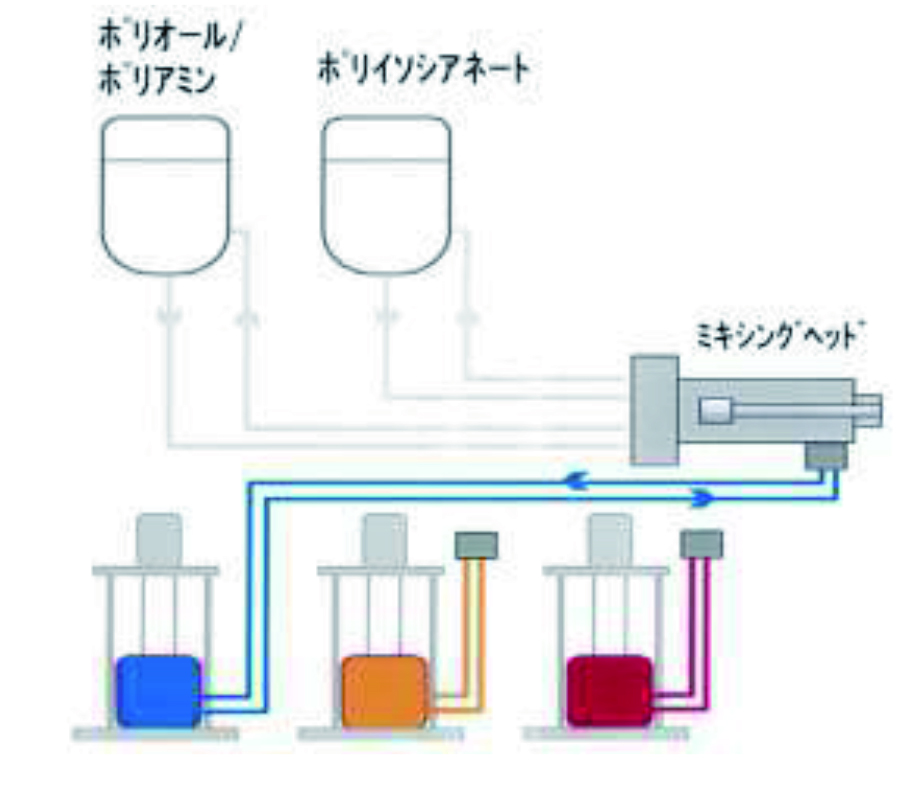
反応型樹脂注入機のイメージ
プロセス、材料、金型と三位一体
今回GSIクレオスが提案している型内塗装は、独Krauss Maffei社の成型技術ノウハウをベースに、100%子会社のKrauss Maffei Japanがコア技術のウレタン注入機の国内製造を担う。
塗料は型内用コーティング材で先行しているRuehl社(ドイツ)製品。武蔵塗料が2019年に同社と型内塗装における事業アライアンス契約を締結していることから、国内の試作、量産のサポートや調色等は武蔵塗料が行う。また、成形試作を含む金型の設計、製造を岐阜多田精機が担当している。 新しい塗装プロセスである型内塗装の実現には、「プロセス、材料、金型と三位一体となり部品を製造することがポイント」(GSIクレオス・古賀拓也氏)とのことだ。
初期投資(金型設備+樹脂注入機等)は近年、自動車内装分野で省エネルギー化や耐傷つき性向上のニーズを受けて適用が広まりつつあるUV硬化プロセスと比べると、約15%高くなるが、某ユーザーの試算では直接作業者数が9.5人から1.5人へ削減、生産歩留まり約22%改善等(ドアトリム、年間20万セット等、膜厚0.4㎜等の一定条件)の経済的メリットは高く、生産単価を下げることで欧州の採用企業では設備投資分を回収している。
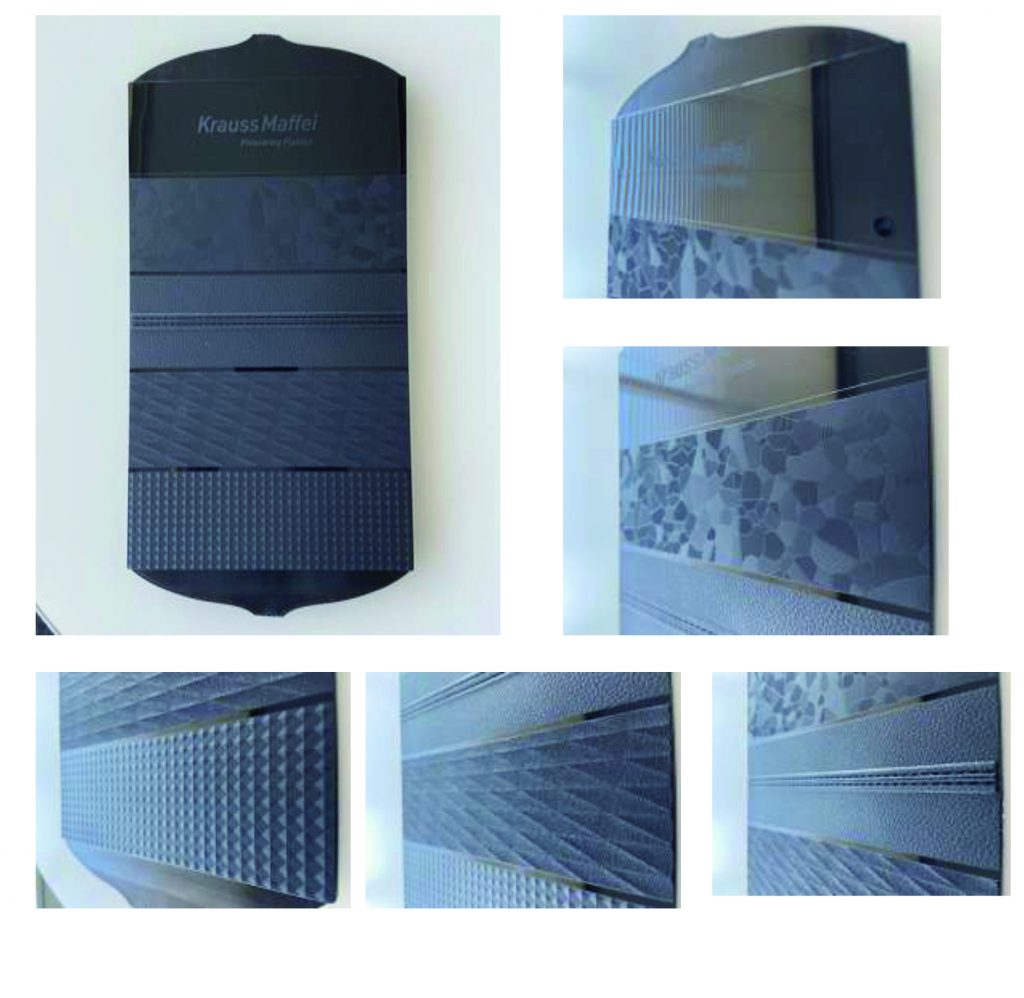
型内塗装で意匠性の幅も広がる
既に欧州車では、メルセデスベンツ、BMW、フォルクスワーゲン等の内外装部品に採用されている。採用の理由には、工程短縮、環境負荷低減の他に型内塗装の意匠性が挙げられる。高光沢ミラー表面仕上げや、マット仕上げに縫い目を施した仕上げなどデザイン幅も広がる。今年投入されたBMWの新型「X5」の内装にも型内塗装が採用されているそうだ。
現在、型内塗装はスペシャリティ領域での採用が主だが、高い歩留まり率や環境負荷の低減から、将来は型内塗装がコモディティ化する可能性もある。住宅建材や白物家電への展開も今後予想されている。